Understanding Small Block Chevy
Cylinder Head Variations
Historical knowledge is important and interesting! The Chevrolet small block was one of the first engines that the aftermarket began designing and manufacturing cylinder heads for. If fact, General Motors as “GM Performance Parts”, now known as “Chevrolet Performance” helped drive the development. Founded in 1967, GM Performance Parts was created to support the Trans-Am Camaro race teams by selling GM-manufactured and branded performance products to the general public.
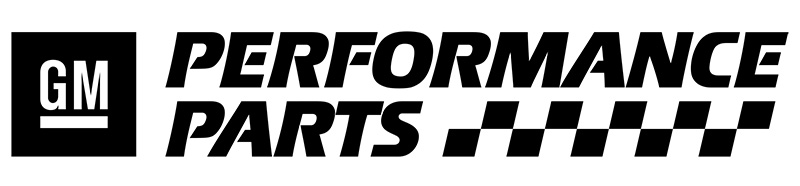

It was the year 1955 when the first small block Chevrolet engine was introduced to the world. The 265 cubic inch V8 engine was released in the 1955 Bel-Air and Corvette and offered two versions with ratings of 162 and 180 horsepower. The difference was due to the camshaft and carburetor size. By 1957 the small block was now a 283 cubic inch engine with horsepower ratings of 185 to 283. The 1957 Chevrolet Corvette with 283 horsepower was the first engine to produce one horsepower per cubic inch. A milestone that built a foundation of future performance gains.
Jump forward a decade and beyond and engine builders, race teams, car crafters, street-rodders, and enthusiasts would search salvage yards for specific casting numbers and cylinder head identifiers. Our search would focus on the last three digits of the casting number or the cast identifier at the end of the cylinder head. The terms “fuelie”, “double-hump”, and “camel hump” were often used to describe some identifiers. However, these were merely a quick external peak at what a person may hope to find with a desirable casting number. The casting numbers were more accurate, and many identifiers were the same across multiple casting numbers.
As GM started to developed performance aftermarket cylinder heads, beginning with the 292 “turbo head” in the 1970’s and then the Bowtie heads in the early 1980’s, aftermarket cylinder head manufacturers began to appear. By the mid to late 1980’s numerous companies were manufacturing small block Chevy cylinder heads, including Canfield, World Products, Dart, Brodix, AFR, and others.
The majority of these over-the-counter cylinder head offerings were still largely based on original GM castings. Improvements were developed through thousands of hours of porting, testing, modifying, and retesting.
These early performance offerings were still mostly made from cast iron due to the high cost of aluminum. Performance improvements occurred by making changes to port shape and volume, chamber design and volume, valve pocket improvements, and valve size compatibilities. These performance developments forced fundamental changes in the overall manufacture of the cylinder heads. Thicker decking provided improved sealing force. Additional casting thickness in other critical areas provided reinforcement for durability and additional modifications. These changes affected and often benefited the water jackets for improved cooling and thermal dispersion. Impurities, such as titanium and aluminum were reduced. Increased levels of phosphorus benefited flowability of the molten materials during the casting process. Increasing the nickel content improved structural balance, impact strength, and hardenability.
Although improvements in cast iron manufacturing helped bring in new cylinder head manufacturers, offering a broad range of new products, aluminum was about to take over.
In a very short period of time aluminum cylinder heads became the standard. This was due to a high demand for weight savings, easier machining processes and repair capabilities. Additionally, machining improvements, including the availability of automated computer numeric controls (CNCs); advancements in metallurgy offered stronger and lower-cost cast aluminum production, and billet materials shortly after — aluminum cylinder heads were beginning to take over the industry.
Jumping Ahead (pun intended)
Almost overnight, dozens of cylinder head manufacturers appeared. Cylinder head designs boasted various runner volumes, raised ports, unique port shapes, changes in spark plug locations and angles, larger valves, longer valves, shorter valves, various rocker arms, valve springs, cooling, and accessory component configurations and capabilities.
Almost anyone with access to a computer, the right design software, a 3-D modeling or scanning program, and CNC machining capability could design and manufacture their own cylinder heads.
Similarities and near copies of cylinder head designs began to appear. Companies focused on anything that could make their product offering unique, either legitimately by extensive research and development or through gimmicks. To compete, some companies would provide airflow test values that did not use the standard 28″ of water making it harder to compare against a similar competitive product.
Legendary engine builder Smokey Yunick started using 28″ of water, or about 1 psi, for flow testing and it became the unofficial standard. I do not know if this was due to his equipment capability (consistent air pressure and flow generation) or for some other reason, but it stuck.
Dyno test engines were carefully assembled using specific and complimentary product selection (camshafts, compression, etc.) to ensure a marketable horsepower and torque improvement that generated consumer interest.
These new and unique cylinder head designs started to cause problems for exhaust header manufacturers who were trying to offer a wide range of compatible products to their customers.
Exhaust Header Compatibility
Consider these variables when designing and manufacturing an exhaust header set. Each of the groups below affect header design and application compatibility. The optimum header addresses each of these groups with limited compromise.
First, the Vehicle Application:
- Car, Truck, 2wd, 4wd, specialized
- Stock chassis or aftermarket
- Engine swap?
- Steering type
- Transmission
- Air conditioning or other accessories
- Ground clearance
- Intended use (cruiser, street rod, racing, towing, RV)
- If racing, what type?
General Engine Specs:
- Engine brand and type
- Engine size
- OE block or aftermarket
- Standard deck height or tall deck
- Oil pan type and dipstick location
- Power and Torque output
- Average operating RPM
- Peak operating RPM (racing)
- Sensor requirements (O2, knock, etc.)
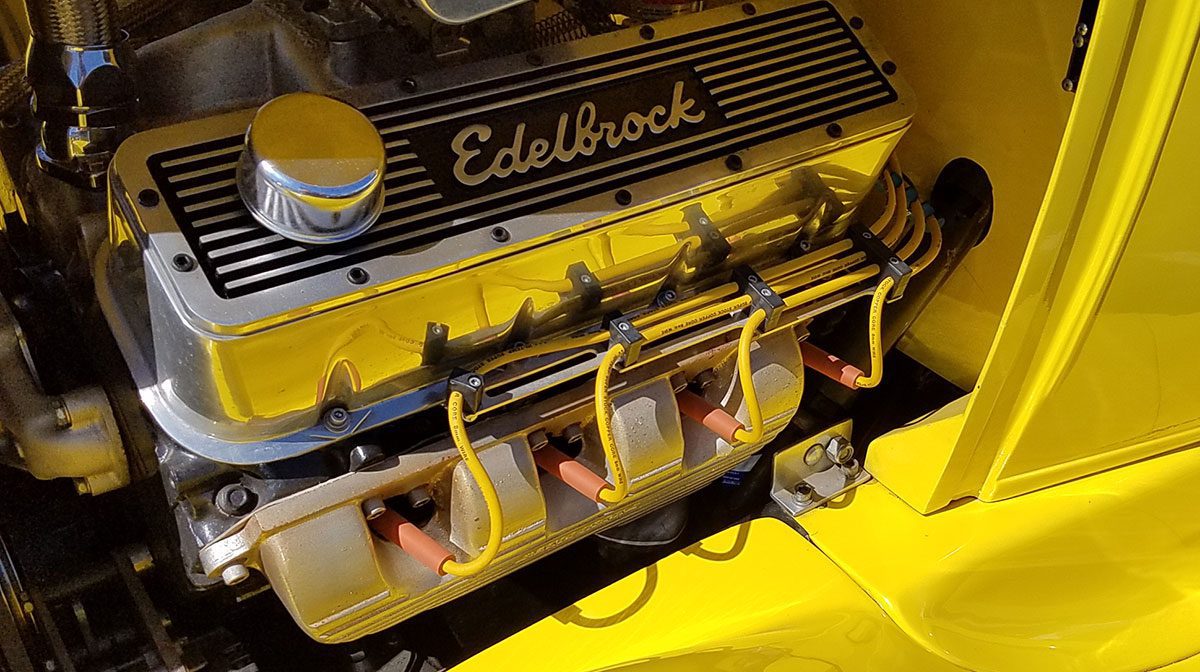
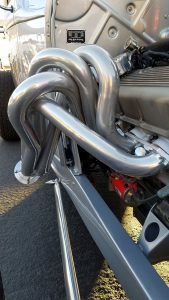
What Type of Header is Required?
- Inside Chassis
- Full length
- Mid length
- Shorty
- Fenderwell
- Outside Chassis
- Zoomie
- Classic Side Pipe
- Lakes Style
- Custom
- Material & Design
- Cast Series
- Tube-Style
- Tube Size
- Thick or Thin Flange Design
- Inside Chassis
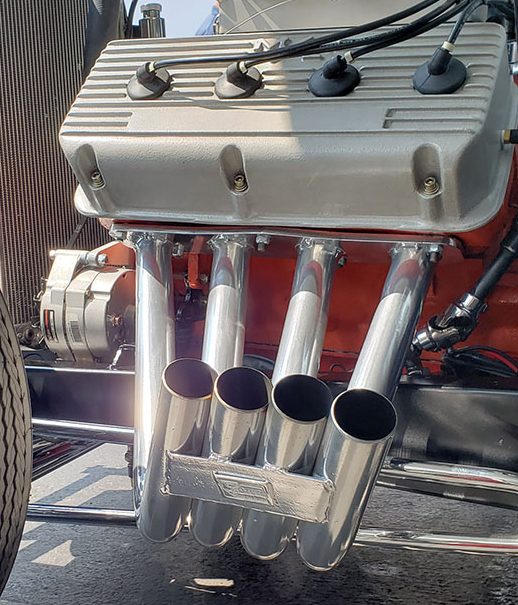
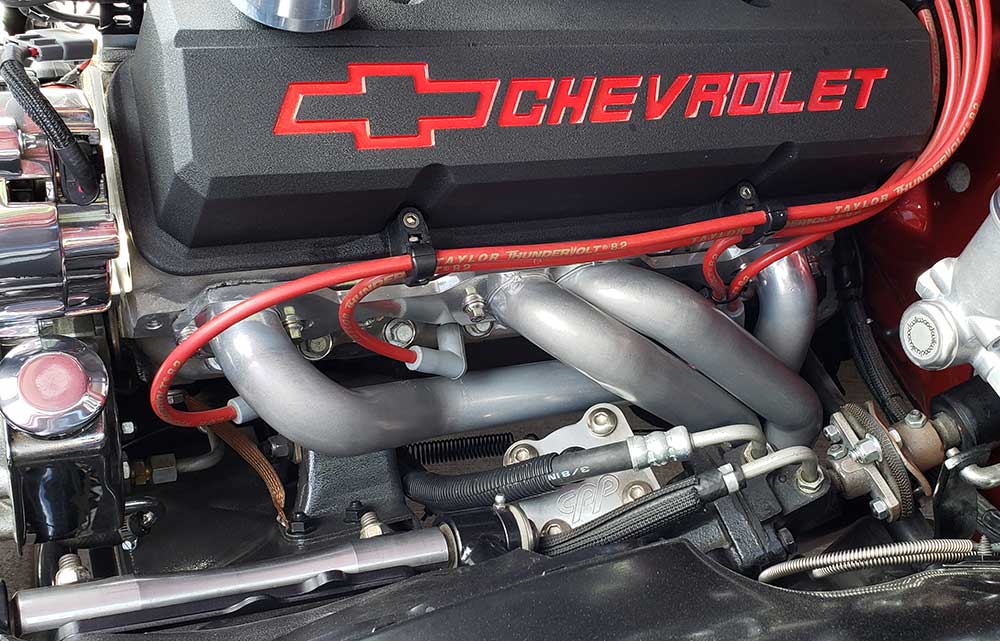
The Focus of This Article - Cylinder Head Variables
The cylinder head choice can cause problems finding the optimum header for an application. Although I am presenting the cylinder head selection as the fourth variable group, it can often be the determinant factor whether or not a compatible header set is available for the application. Each is explained in more detail below.
The exhaust port shape and dimensions are often primary concerns for many customers because we have been told for decades that it is important for the header flange to match the exhaust port. This is not 100% true. On an application spending most of its time high in the RPM range (over 6,000 RPMs) and those looking for every last 1/4 horsepower, port matching can provide benefit. For the average street rod, daily driver, truck, or RV it is insignificant. There is not enough airflow volume to make port match a factor beyond some of us being overly anxious about it.
What matters more in these applications is proper sealing of the header flange against the cylinder head. Many header manufacturers will use the same flange design and port shape across a broad range of applications. This is perfectly acceptable! For example, most header brands will state in their application compatibility that their headers are “compatible with GM ZZ4 and similar D-port cylinder heads.” This is absolutely correct. The flanges on these headers will cover (partially block) the uppermost portion of the exhaust port. Again, this is not a serious issue and should not be a concern for most applications.
For Sanderson Headers and their patented raised flange sealing design, ensuring the use of the proper port flange becomes crucial. Below are the most common port shape examples for small block Chevy cylinder heads.
It is critical for Sanderson Headers to have adequate sealing area on the cylinder head. Using the image above as a guide, in most cases a standard round or square port flange will not seal properly on the D-port cylinder head opening. The same is true for a D-port flange that will not be able to seal on a common round, square, or d-shaped port opening.* This is why it is important to select the correct flange design for Sanderson Headers on a small block Chevy engine.
*There are a few exceptions when the cylinder head has a fully machined exhaust side. This is common on billet cylinder heads. See the Sealing Surface topic below.
Along with exhaust port shape, port dimensions can sometimes affect header choice. This is often a problem when the customer believes that the header port dimension should match the port dimensions on the cylinder head. Again, this is should only be a concern on racing applications operating at high RPM when the airflow speed and volume justify it. In one example, say we have a cylinder head port width of 1-5/8″ but the header port opening is 1-1/2″. There is no reason to stress over this. That is a mere 1/16″ per side and is not going to dramatically affect an engine that is operating primarily below 4,000 RPM.
Flange port size is directly related to the primary tube size of the header. The port opening in the flange must be compatible with the tube size and vice-verse. If the flange opening is too large or too small for tube size used on the header it affects both the manufacturing process and final size of the completed port opening. The overall port dimension is also affected by the swaging and welding methods.
Many header manufacturers form a starter tube into the header flange. Sanderson Headers actually use a fabrication technique that eliminates the need for a starter tube. This is why Sanderson Headers fit so snugly to the engine.
A swaging machine is one common method of fitting the tube to the port flange. However, some header designs require manual swaging by hammer, a forming jig, and dolling tools. A raw header flange with a port opening that is considerably too large or too small for the tubing can create an inefficient final product.
Since we are dealing with different exhaust port shapes and tubing sizes, the final port dimensions vary by application.
Again, the focus on most applications is proper sealing. If the header port is slightly smaller than the exhaust port, don’t worry too much about it. If the header port is too large it is OK to be a little concerned about a potential increase in exhaust gas reversion. This is one of the reasons why talented engine builders often suggest headers with a smaller primary tube diameter for their customers. Most street engines operate more efficiently (hint: this means more power and torque) using a header matched to operate between idle and 4,000 RPM — where the engine is going to spend most of its time.
The exhaust port exit location on the small block Chevy cylinder head can cause issues with header compatibility. There isn’t a problem when the exhaust port resides in the neutral, original General Motors position.
There are many aftermarket cylinder heads designed with a raised exhaust port. This describes having exhaust ports with a more gradual exit arc that moves the exit point further up the side of the cylinder head. An average raised port head can relocate the port exit by small amount to as much as 0.500″.
Moving the exhaust port up will also raise the header up the same amount. However, it also moves the header location outward slightly due to the exit angle of the cylinder heads. This may cause new clearance problems with frame rails, shock towers, suspension, and steering components.
Additionally, another concern is a header design with a tube running parallel to the cylinder head and under the spark plugs. A raised port cylinder head will bring this tube closer to the spark plugs. Dimpling of the tube would be required at any location that did not allow adequate clearance for the plug wire boot.
Aside from specific vehicle application compatibility and the list of variables listed above, it is spark plug location causes the most grief for small block Chevy header manufacturers.
Straight plug or angle plug descriptions are quite vague for what is sometimes a more complex concern.
A straight plug cylinder head can be manufactured in a variety of locations and still be considered a straight plug head. For example, original GM cylinder heads have a spark plug location and vertical angle that is different from GM Vortec, Trick Flow, BluePrint, and other aftermarket heads.
Angle plug cylinder heads have even more variations. Original GM heads like the 492 casting vary from the GM 292 Turbo heads, GM Bowtie, Brodix Track 1, RHS, and numerous other examples exist.
It is common to see a header set advertised as compatible with straight plug heads, angle plug heads, or both. Some manufacturers will include more specific details on cylinder heads that are compatible, or are not compatible. The problem is that there are so many different small block Chevy cylinder head choices that it is impossible for a header manufacturer to keep up with every possible brand and part number available.
Sometimes a customer will not know if a header set is compatible with their cylinder heads until test-fitting it on the engine. Of course, this is frustrating, but it occurs based on everything discussed in this article.
The final consideration is somewhat specific to Sanderson Headers’ patented raised flange design. Small block Chevrolet cylinder heads have one of two exhaust surface styles. See graphic below.If using the wrong flange style on the stepped sealing surface it is possible that the Sanderson raised flange will not have cylinder head material to seal against, causing a substantial exhaust leak. For example, using a D-port flange on a standard port head, or a standard flange on the D-port head.
The flat machined surface is less likely to have this problem, but it can still occur. If the cylinder head has a very large port opening and the raised flange surface does not extend far enough around the port, a sealing problem will occur.
To Summarize
Cylinder head choice for small block Chevy engines can cause problems finding the right exhaust header for the application. The best way to reduce the possibility of problems is to perform a bit of research and ask questions. The last thing anyone wants to do is build the perfect engine and chassis of our dreams only to find out that no one makes a set of headers that will fit the combination.
Here are a few examples of common problems.
- On most 1955-57 Chevy (Tri-Five) cars, selecting the correct header is a process of elimination. Going down the list of incompatibilities (steering type, transmission, and spark plug angle), and suddenly there are no more options. Cylinder head choice can be critical for these vehicles.
- BluePrint crate engines. BluePrint recommends Sanderson, Hedman, and Lemons Headers for their engines. Although I’m not certain what Lemons is doing, Hedman and Sanderson are not making BluePrint-specific headers. Hedman is the luck of the draw for plug clearance, and Sanderson is applying any necessary tube dimpling for spark plug boot clearance if they know when the order is placed that their headers are going on a BluePrint engine (or Vortec-based cylinder head).
- There are some cylinder heads that make header manufacturers cringe. This is often due to spark plug angles and/or locations. On some applications it is possible to make subtle modifications to achieve compatibility. Trick Flow heads for example require modifications to the bottom of the header flange for clearance and spark plug access. On some cylinder heads it is nearly impossible to find a header set that does not require drastic modifications. The Brodix Track 1 and RHS heads are prime examples.
There is a dimension that can help Sanderson Headers determine whether a header is compatible with some straight plug cylinder heads. The image below shows an example of measuring the distance between the center of the threaded spark plug hole and the center line of the exhaust port.
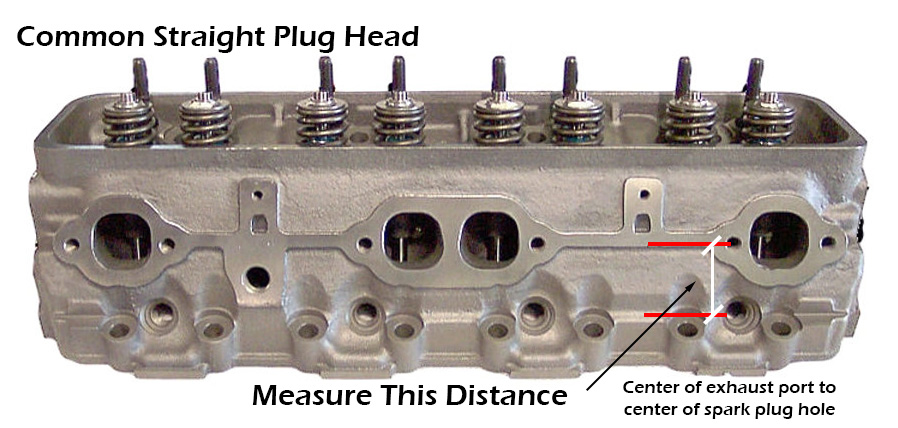
If unsure about the best header choice for your application, please ask.